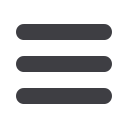
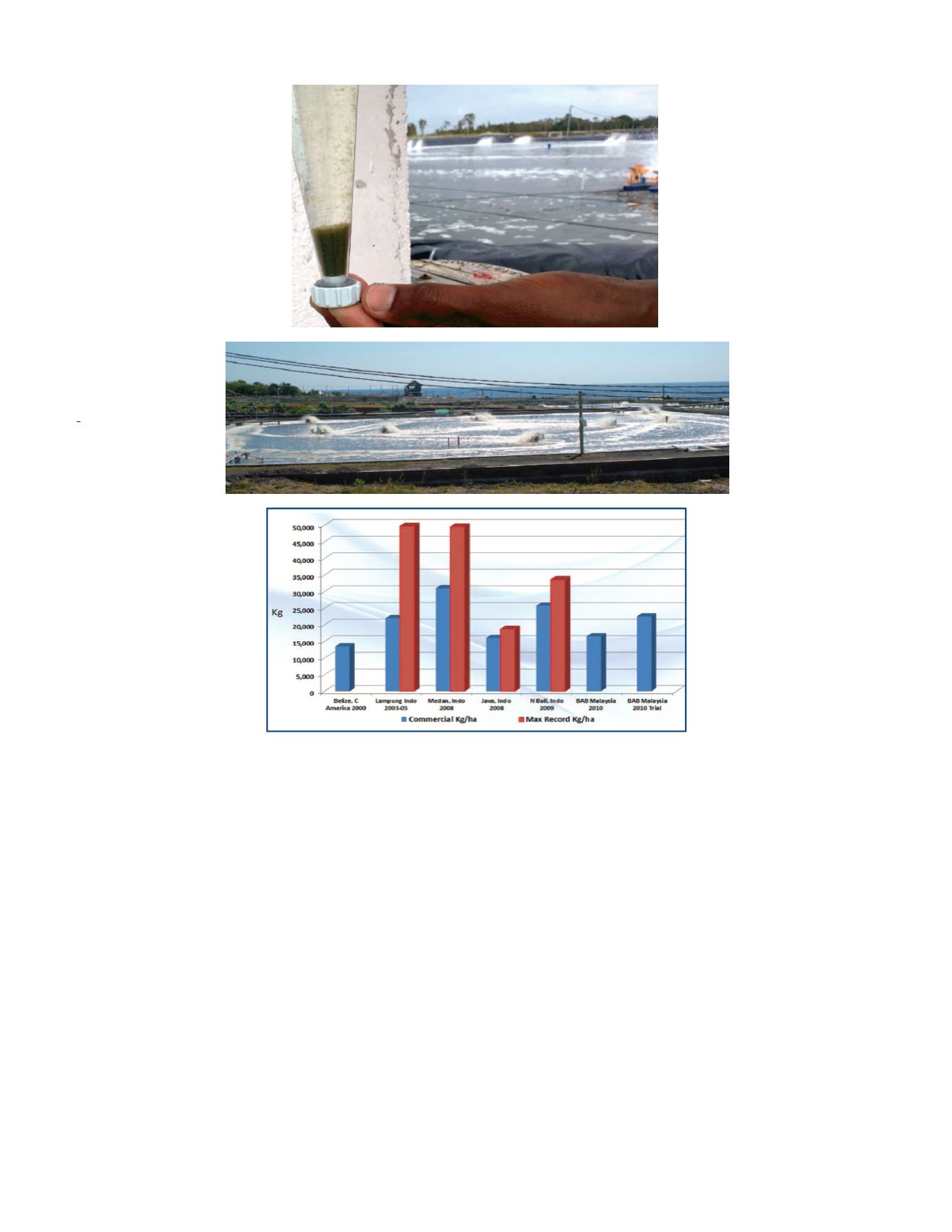
•
WORLD AQUACULTURE
•
DECEMBER 2014
25
(29-30 percent) feed. Grain pellets
and molasses supply carbon as
needed to sustain carbon-to-
nitrogen ratios greater than 15.
Generally grain pellet applications
vary from 15 to 20 percent of the
total feed used during operations.
Molasses can be applied two or
three times weekly at 15-20 kg/ha.
Water stability of grain pellets is
between 15 and 20 minutes. This
provides an inexpensive organic
substrate for biofloc
to develop, in addition
to increasing the C:N
ratio.
Grain pellets are
a mixture of ground
wheat, corn and
occasionally soy, with
a protein level around
14-18 percent. Animal-
grade ground wheat
flour must be used. Using
grain pellets from wheat flour
as a carbon source results in
better yield, survival and FCR
of green tiger shrimp
Penaeus
semisulcatus
(Megahed 2010).
In addition to typical
chemicals such as dolomite
and lime, kaolin is required in
the preparation of pond water
and during operation. Kaolin
is the mineral kaolinite, a
hydrous aluminum silicate,
also known as China clay. It
is distinguished from other
industrial clays on the basis of
its fine particle size and pure
color. Its ability to disperse in water makes it an ideal pigment. Fine
particles of kaolin suspended in pond water are thought to become
nuclei of bioflocs in pond water. Kaolin is applied at 50-100 kg/ha.
Aerators help suspend bioflocs continuously in the pond water,
a main requirement for maximizing the potential of microbial
processes in shrimp culture ponds (Fig. 5). Especially in biofloc
systems, aerators need to be constantly monitored for malfunctions
and repaired or replaced without delay. Paddlewheel aerators keep
dissolved oxygen levels high. Dissolved oxygen levels must be
monitored frequently to keep levels greater than 4 mg/L. Water
quality should be managed within the limits indicated in Table 2.
Paddlewheel aerators need to be in the correct position
to promote accumulation of sludge in central areas of ponds.
Accumulated sludge at the pond center needs to be siphoned or
drained out periodically as needed. The required energy input
(horsepower of aerators) needs to be correlated to stocking density.
High stocking densities of 130-150 post-larvae/m
2
and high aeration
rates of 28-32 hp/ha are also
essential for expected production
of over 20 t/ha. Aeration
energy efficiency is 680 kg/
hp and can be as high as 1,000
kg/hp if partial harvesting is
implemented.
Performance of Biofloc
Systems in Commercial
Shrimp Farming
The technology has been
successfully applied
commercially
with shrimp
(L.
vannamei)
by
Belize Aquaculture
(McIntosh 2001).
Heterotrophic
bacterial
communities
facilitate the
production of high
yields (~15 t/ha per cycle)
in ponds with no water
exchange. It has also been
applied with success in
commercial shrimp farming
in Indonesia, achieving a
production of nearly 50 t/
ha in small research and
development ponds, and over
20 t/ha from commercial
ponds, with feed conversion
ratios between 0.98 and 1.30
(Table 3; Kopot and Taw
2004, Taw 2005, Taw 2010).
A combination
of two technologies,
partial harvesting and
biofloc, has been studied in northern Sumatra, Indonesia (Taw
et al.
2008). Production performance using partial harvest with
biofloc technology was greater than expected. One 2,500-m
2
pond produced 12.4 t (49.5 t/ha) through six partial harvests, with
a feed conversion ratio of 1.11. The technology was successfully
commercialized in Malaysia (Taw
et al
. 2011). For ponds lined on
dikes only, the shrimp farm averaged over 12 t/ha; for fully-lined
ponds with a semi-biofloc system, the average was over 16.2 t/
ha. Two ponds with biofloc systems averaged over 22.5 t/ha with
an average shrimp size of approximately 18 g. The outstanding
achievement was in a biofloc system with a stocking density of 130
post-larvae/m
2
, where shrimp reached over 18.8 g in just over 90
days of culture, with a production of over 22.5 t/ha (Taw
et al
. 2011).
A similar performance with a semi-biofloc system was recorded at
the iSHARP project in Malaysia (Taw
et al
. 2013, Fig. 6).
The small, family-owned Ndaru Luat Setio shrimp farm
( C O N T I N U E D O N P A G E 2 6 )
TOP, FIGURE 4.
About 5 mL/L of settled biofloc in an Imhoff cone. Moderate floc
densities are preferable.
MIDDLE, FIGURE 5.
Biofloc shrimp culture ponds must be
well aerated. Note number and positioning of aerators.
BOTTOM, FIGURE 6.
Shrimp
production in commercial-scale biofloc systems.