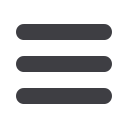
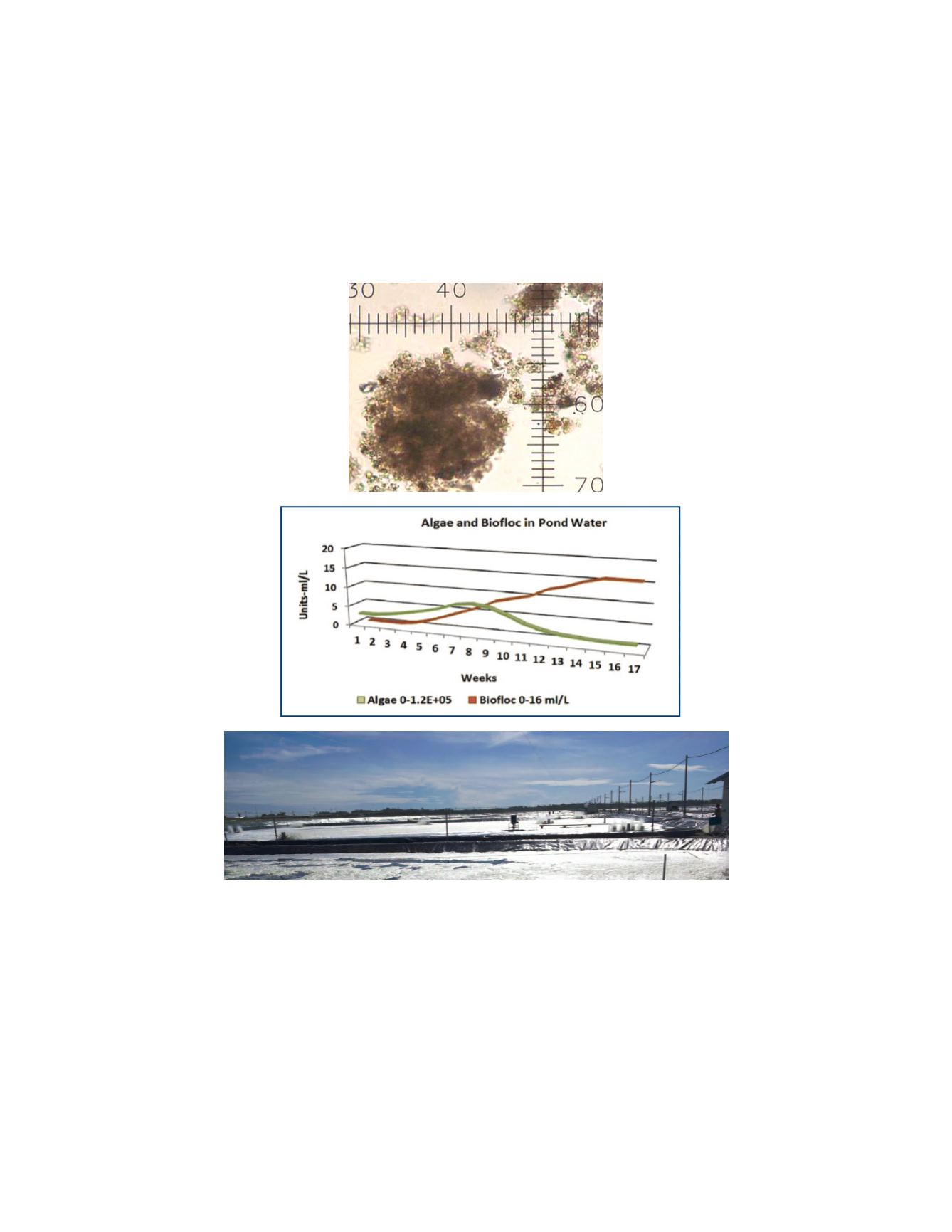
24
DECEMBER 2014
•
WORLD AQUACULTURE
•
WWW.WA S.ORGB
iofloc systems—a recent
technology—offer a promise of stable
and sustainable production, inasmuch
as the system is operated without water
exchange and so has an enhanced capacity
for nitrification within the culture ponds
(Avnimelech
et al.
2012). The main
economic advantages of biofloc technology
over greenwater (algae-based) systems
are higher growth rate, lower FCR and
sustainable production (Table 2).
Bioflocs are
macroaggregates – diatoms,
macroalgae, fecal pellets,
exoskeletons, remains of
dead organisms, bacteria, and
invertebrates – suspended in the
water column (Fig. 1). Biofloc
can be used as a single-cell
protein source for shrimp and
fish. The crude protein content
of biofloc ranges from 35 to
50 percent, and the crude lipid
content is 0.6 to 12.0
percent by volume.
Biofloc can be slightly
deficient in arginine,
lysine and methionine.
The ash content ranges
between 21 and 32
percent.
In biofloc
systems, algae develop
first, then a transition
period with foam
formation and finally
a brown biofloc
develops (Fig. 2 and 3).
This may take a few weeks or longer, depending on the biomass of
shrimp or fish in the pond. The transition occurs earlier with tilapia,
later with shrimp. Basically the systems starts with an algae bloom
and the biofloc community develops thereafter.
Advantages and Disadvantages
One of the main advantages of biofloc technology is high
biosecurity. To date, white spot syndrome virus has not been a factor
in biofloc systems. Production and carrying capacity are typically
Shrimp Farming with Biofloc
Technology: Commercial Experience
and Approaches to Disease Control
Nyan Taw
5-10 percent greater than in typical culture
systems with no water exchange. Shrimp
grow larger and reflect feed conversion
ratios between 1.0 and 1.3. Production
costs can be 15 to 20 percent lower.
A main disadvantage is the high
energy input for aeration. Power failures
of more than one hour in duration can be
critical. Biofloc ponds need to be lined.
The more advanced technology also
demands better training of technicians.
Brief Operating
Protocol for
Shrimp Farming
Biofloc technology
for shrimp culture on a
commercial scale and in
large ponds is simple and
yet, in a way, complex. Basic
conventional procedures,
depending on location and
situation of the farm, need
to be followed. The
procedure must
be adjusted with
changes in culture
water environment
and shrimp behavior,
such as health and
growth (Table 1).
For optimized,
sustainable
commercial biofloc
shrimp culture,
HDPE- or concrete-
lined ponds are basic
requirements. Only
specific pathogen-free post-larvae are stocked.
When ponds are stocked, a major factor to be controlled is
biofloc volume. Using Imhoff cones for assessment, biofloc volumes
must be maintained below 10 mL/L for full biofloc and 5 mL/L for
semi-biofloc systems (Fig. 4). A sample must be taken concurrently
from each of two locations below the water surface. Green or brown
water is acceptable, but black water is an indicator of abnormal
conditions. Suspended biofloc must be available as food for shrimp.
Shrimp can be fed high protein (35-40 percent) or low protein
TOP, FIGURE 1.
A biofloc macroaggregate.
MIDDLE, FIGURE 2.
Changes in the importance of algae
and biofloc in a production cycle for shrimp. Algae is more important in the first half and biofloc dominates in the
second half in response to high feed loading.
BOTTOM, FIGURE 3.
The transition from algae dominance to
biofloc dominance in biofloc shrimp ponds is indicated by the presence of abundant foam.